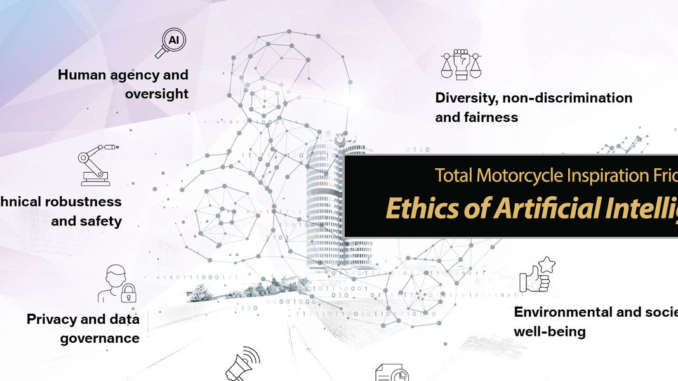
The Social Dilemma. Google, Twitter, Facebook, TikTok, Huawei, WeChat, Apple AI. Corporation AI. Take a deep dive with TMW into our Inspiration Friday Ethics of Artificial Intelligence special. Artificial Intelligence surrounds us, when you turn on your TV, use your Smartphone, drive your Car, go to Work, it is this invisible world that influences everything in your daily life. How, Why and should You care?
The short answer is YES, you should care and because you should we as a society need principles covering the development, application, morals and ethics in the use of Artificial Intelligence and Smart Data. BMW defines these as:
- Human agency and oversight.
- Technical robustness and safety.
- Privacy and data governance.
- Transparency.
- Diversity, non-discrimination and fairness.
- Environmental and societal well-being.
- Accountability.
I have heard that the CEO of BMW has been quoted as saying, “I am not the CEO of a car company, I am the CEO of a technology company.” And this article proves it.
Companies generate and use a lot of data. You have probably heard that data is the new oil, and doesn’t that seem true? Data is EVERYWHERE.
AI is fast, reliable and easy to integrate into the various production processes and, coupled with smart data analytics and cutting-edge measurement technologies, it opens up new opportunities for more efficient production such as AI focused, company-wide networking and knowledge transfer. The fundamentally identical technology forms of AI can generate added value for customers, employees and business processes.
What do you think of AI? What morals and ethics would you include? How do you stand on its use?
Here are just a few of the fascinating things we are already doing with Artificial Intelligence, Smart Data and Virtual Reality human augmentation:
- Robotics applications out-perform the technology used previously in their coordination skills and ability to recognise people and objects.
- AI incorporates context information into the search process, enabling it to flag up identical and similar cases.
- Chatbots help to significantly increase the quality and availability of customer service. In China, BMW Financial Services offers its customers an AI-based chatbot via the widely used WeChat app.
- AI is the key to automated driving – they can take over longitudinal and lateral guidance of the vehicle for extended periods. The customer remains responsible for the car, but their task is now only to monitor what is happening. The Intelligent Personal Assistant increasingly allows the car to be operated, functions to be accessed and information obtained by voice command alone. This technology enables direct communication and natural interaction with the vehicle – helped by AI.
- It takes about 30 hours to manufacture a vehicle. During that time, each car we make generates massive amounts of data. With the help of artificial intelligence and smart data analytics, we can use this data to manage and analyse our production intelligently.
- AI helps streamline manufacturing even further….and saves our employees from having to do monotonous, repetitive tasks.
- At Plant Munich because we have the sensors and collect their data in a cloud, we can now monitor round-the-clock whether any maintenance work is needed.
- Radio Frequency Identification (RFID) allows components to be identified automatically and contactlessly throughout the value chain.
- Special robots: The advantages of the system are obvious: “This robot is not only much faster, it’s also more precise. The results we obtain are highly detailed and, most importantly, objective.
- Virtual reality already plays an important role in planning logistics spaces.
Seven principles covering the development and application of artificial intelligence at the BMW Group:
- Human agency and oversight.
The BMW Group implements appropriate human monitoring of decisions made by AI applications and considers possible ways that humans can overrule algorithmic decisions. - Technical robustness and safety.
The BMW Group aims to develop robust AI applications and observes the applicable safety standards designed to decrease the risk of unintended consequences and errors. - Privacy and data governance.
The BMW Group extends its state-of-the-art data privacy and data security measures to cover storage and processing in AI applications. - Transparency.
The BMW Group aims for explainability of AI applications and open communication where respective technologies are used. - Diversity, non-discrimination and fairness.
The BMW Group respects human dignity and therefore sets out to build fair AI applications. This includes preventing non-compliance by AI applications. - Environmental and societal well-being.
The BMW Group is committed to developing and using AI applications that promote the well-being of customers, employees and partners. This aligns with the BMW Group’s goals in the areas of human rights and sustainability, which includes climate change and environmental protection. - Accountability.
The BMW Group’s AI applications should be implemented so they work responsibly. The BMW Group will identify, assess, report and mitigate risks, in accordance with good corporate governance.
Overall centre of competence for the company: “Project AI”.
“Project AI” was launched in 2018 to ensure that AI technologies are used ethically and efficiently. As the BMW Group’s centre of competence for data analytics and machine learning, it ensures rapid knowledge and technology sharing across the company. Project AI therefore plays a key role in the ongoing process of digital transformation at the BMW Group and supports the efficient development and scaling of smart data and AI technologies. One of the developments to come out of Project AI is a portfolio tool which creates transparency in the company-wide application of technologies making data-driven decisions. This D³ (Data Driven Decisions) portfolio currently spans 400 use cases, of which more than 50 are available for regular operation.
WHERE IS THE BMW GROUP ALREADY USING AI?
USE CASES FROM DIFFERENT AREAS OF THE COMPANY.
The following examples show that Project AI pushes the BMW Group forward with AI focused, company-wide networking and knowledge transfer. The fundamentally identical technology forms of AI can generate added value for customers, employees and business processes. For example, the customer benefits from natural language processing (NLP) with the Intelligent Personal Assistant directly in the vehicle and employees are supported with translation tools and context-processing assistants in administrative processes. Intelligent data analysis and machine learning are used to optimise energy management both in buildings and in vehicles. And image processing AI relieves both the customer with driver assistance systems from monotonous driving tasks and employees in production from monotonous processing steps.
E XAMPLES FROM RESEARCH & DEVELOPMENT.
AI-based energy management in vehicles.
A vehicle contains a large number of electric consumers, such as seat heating, the entertainment system, the air conditioning, etc. In many cases, the driver is not aware that using these consumers also has an effect on CO2 emissions and/or the range of the vehicle. AI experts at the BMW Group are conducting R&D work on AI-based software for in-vehicle energy management. Taking user behaviour and route information as a basis, the system learns how to adjust energy consumption in the car as effectively as possible to the driver’s requirements and the need for energy efficiency. In this way, CO2 emissions can be reduced, energy saved and operating range increased.
Acoustic analytics: sensory enhancement in the sensor model for automated driving functions.
The BMW Group is taking an all-encompassing approach to monitoring the vehicle environment. One of the areas the company is exploring to this end is how acoustic signal processing can be added to the AI sensor fusion. Incorporating auditory perception can have benefits for urban scenarios, in particular, going forward.
AI in requirements management.
At the BMW Group there are over 33,000 requirement specification documents containing more than 30 million individual requirements for vehicles, components and characteristics. That’s an enormous amount of data. AI technologies can help employees to process large quantities of data more quickly and carefully. Here, an application has been developed which uses natural language processing methods to improve the quality and analysis of individual requirements in specification documents. The web-based tool allows thousands of requirements to be automatically translated and checked – in real time – for linguistic quality, similarity and consistency.
EXAMPLES FROM SUPPLY CHAIN MANAGEMENT AND LOGISTICS.
Integrating AI with facility and robot control systems.
The first smart AI control application at the BMW Group celebrated its premiere at the BMW Group’s Steyr plant. This application speeds up logistics processes by preventing the unnecessary transport of empty containers on conveyor belts. To this end, the containers pass through a camera station. Using stored image data marked by employees, the AI application recognises if a container needs to be lashed onto a pallet or whether – in the case of large, stable boxes – no additional securing is required. If no lashing is required, the AI application directs a container by the shortest route to the removal station for the forklift truck.
Besides the application in Steyr, AI can be found in numerous other logistics innovations (SEE ARTICLE BELOW) at the BMW Group. It also supports virtual layout planning, which creates high-resolution 3D scans of buildings and factories. AI ultimately contributes to the recognition of individual objects in the 3D scans, such as containers, building structures and machines. In this way, robotics applications out-perform the technology used previously in their coordination skills and ability to recognise people and objects. Navigation improvements enable obstacles such as forklift trucks, tugger trains and employees to be detected more quickly and clearly, and alternative routes to be calculated within milliseconds. The AI-based technology helps the robotics applications to learn and apply different reactions to people and objects.
EXAMPLES FROM PRODUCTION.
Since 2018, the BMW Group has been using various AI applications in series production. One focus is automated image recognition: In these processes, AI evaluates component images in ongoing production and compares them in milliseconds to hundreds of other images of the same sequence. This way, the AI application determines deviations from the standard in real time and checks, for instance, whether all required parts have been mounted and whether they are mounted in the right place. At the BMW Group, flexible, cost-effective, AI-based applications are gradually replacing permanently installed camera portals. Implementation is comparatively simple. A mobile standard camera is all that is needed to take the relevant pictures in the production hall. The AI solution can be set up quickly too. Employees take pictures of the component from different angles and mark potential deviations on the images. This way, they create an image database in order to build a neural network, which can later evaluate the images without human intervention.
Name plate checks.
In the final inspection area at the BMW Group’s Dingolfing plant, an AI application compares the vehicle order data with a live image of the newly produced car’s model badge. Model designation badges and other identification plates (such as “xDrive” for all-wheel drive vehicles and all generally approved combinations) are stored in the image database. If the live image and order data don’t correspond – if a designation is missing, for example – the final inspection team receives a notification.
Dust particle analysis in the paint shop.
AI can control the operation of highly sensitive automotive production equipment even more precisely, as a pilot project in the paint shop at the BMW Group’s Munich plant has shown. If levels of dust increase due to the time of year or a sustained dry period, the algorithm picks up on the trend at an early stage and brings forward the timing of a filter change, for example. Working in conjunction with other analysis tools, additional patterns can be recognised. Another result of the analysis might be that fine adjustments need to be made to the machine using ostrich feathers to remove dust particles from the car body. The BMW Group’s AI experts see great potential in dust particle analysis. Supplied with information from numerous sensors and data from surface inspection, the algorithm monitors more than 160 features of the body and can predict the quality of a paint application with great accuracy. (SEE ARTICLE BELOW)
AI control application in the press shop reliably prevents pseudo-defects.
At the press shop, flat sheet metal parts are turned into high-precision components for the car body. Dust particles or oil residues that remain on the components after forming can easily be confused with very fine cracks, which occur in rare cases during the process. Previous camera-based quality control systems at the BMW Group’s plant in Dingolfing occasionally also identified these pseudo-defects (deviations from the target values, but with no actual fault). With the new AI application, these pseudo-defects no longer occur because the neural network can access around 100 real images per feature – i.e. around 100 images of the perfect component, 100 images with dust particles, another 100 images with oil droplets on the component, etc. This is particularly relevant in the case of the visually close calls that have previously led to pseudo-defects. (SEE ARTICLE BELOW)
BMW won the Connected Car Pioneer Award 2020 in recognition of its versatile use of AI in production (SEE ARTICLE BELOW)
EXAMPLES FROM AFTERSALES & CUSTOMER SERVICE.
AI at dealer service desks.
If a BMW customer visits a dealer reporting a problem with their car, the problem needs to be identified quickly and the right solution found reliably. To help them do this, the service employee has the use of a knowledge database, which has been expanded using a powerful software stack to include both an intelligent and scalable search facility and AI (for processing problem cases and knowledge data). AI incorporates context information into the search process, enabling it to flag up identical and similar cases. Added to which, an automatic translation function breaks down the language barrier in the fault analysis process.
AI-based customer interaction in WeChat.
Chatbots help to significantly increase the quality and availability of customer service. In China, BMW Financial Services offers its customers an AI-based chatbot via the widely used WeChat app. The chatbot allows customers to ask questions regarding their personal finance agreement or make changes to their agreement. These bots are first trained to deal with the topics for which most questions are received by the call centre. If the chatbot cannot answer a question, the enquiry is passed to a human member of staff. This means that customers’ most frequently asked questions can be answered quickly and with a consistently high level of quality around the clock.
EXAMPLE IN BUILDINGS MANAGEMENT.
Increasing energy efficiency in BMW Group buildings.
Since 2006 the BMW Group has been able to consistently increase energy efficiency at its locations around the world. It has now reached such a high level that identifying further potential for improvement using conventional means is getting more and more difficult. This is where the use of smart data and AI comes into play. The BMW Group systematically processes all the energy-relevant data at its locations so previously undiscovered energy consumption patterns can be established using AI. Weather-related data can also be incorporated into this process, enabling buildings to be heated and cooled more intelligently and efficiently. In a pilot project in Munich, this approach has allowed approximately 1,200 MWh of thermal energy to be saved annually in the IT centre. This equates to the energy consumption of approximately 60 family homes. This experience and a rigorous process of data collection and analysis have also led to positive energy efficiency results at office buildings such as the BMW four-cylinder building, FIZ Projekthaus, Campus Freimann and the dynamics centre at Dingolfing.
EXAMPLE FOR ADMINISTRATION & SUPPORT FUNCTIONS.
Customized Machine Translation (CMT) – machine translation that learns the language of BMW.
The BMW Group is a multinational company with a presence in over 100 countries. Its customers, dealers and employees speak hundreds of languages and there is an enormous daily influx of multilingual texts from external sources. Human translation of all multilingual data does not make sense due to the volume and costs involved. Freely available translation solutions are not permitted for reasons of information protection and often fail to provide the correct translation of technical terms and formulations – the correct “BMW language”. With this in mind, BMW Group IT has developed its own translation solution specialising in BMW texts. BMW Group employees are now feeding over 2,000 sentences into the system every day.
EXAMPLES FOR CUSTOMER AND VEHICLE FUNCTIONS.
Driver assistance.
AI is the key to automated driving – and is already present in current driver assistance systems such as Driving Assistant Professional. Automation-based functions help customers to drive safely, park and stay connected. On motorways, they can take over longitudinal and lateral guidance of the vehicle for extended periods. The customer remains responsible for the car, but their task is now only to monitor what is happening.
BMW Intelligent Personal Assistant.
The BMW Group has revolutionised driving pleasure with the BMW Intelligent Personal Assistant. Introduced in 2019, this intelligent digital on-board companion responds to the prompt “Hey BMW”. The BMW Intelligent Personal Assistant increasingly allows the car to be operated, functions to be accessed and information obtained by voice command alone. This technology enables direct communication and natural interaction with the vehicle – helped by AI.
BMW Group applies AI solutions to increase paint shop quality
Artificial intelligence can bring even greater precision to controlling highly sensitive systems in automotive production, as a pilot project in the paint shop of the BMW Group’s Munich plant has demonstrated.
Despite state-of-the-art filtration technology, the content of finest dust particles in paint lines varies depending on the ambient air drawn in. If the dust content exceeded the threshold, the still wet paint could trap particles, thus visually impairing the painted surface.
“Data-based solutions help us secure and further extend our stringent quality requirements to the benefit of our customers. Smart data analytics and AI serve as key decision-making aids for our team when it comes to developing process improvements. We have filed for several patents relating to this innovative dust particle analysis technology,” explains Albin Dirndorfer, Senior Vice President Painted Body, Finish and Surface at the BMW Group.
Two specific examples show the benefits of this new AI solution: Where dust levels are set to rise owing to the season or during prolonged dry periods, the algorithm can detect this trend in good time and is able to determine, for example, an earlier time for filter replacement. Additional patterns can be detected where this algorithm is used alongside other analytical tools. For example, analysis could further show that the facility that uses ostrich feathers to remove dust particles from car bodies needs to be fine-tuned.
The BMW Group’s AI specialists see enormous potential in dust particle analysis. Based on information from numerous sensors and data from surface inspections, the algorithm monitors over 160 features relating to the car body and is able to predict the quality of paint application very accurately. This AI solution will be suitable for application in series production when an even broader database for the algorithm has been developed. In particular, this requires additional measuring points and even more precise sensor data for the car body cleaning stations. The AI experts are confident that once the pilot project at the parent plant in Munich has been completed, it will be possible to launch dust particle analysis also at other vehicle plants.
From press shop to validation: BMW Group Plant Munich builds on artificial intelligence and smart use of data
BMW Group Plant Munich is making increasing use of applications with artificial intelligence (AI). AI is fast, reliable and easy to integrate into the various production processes and, coupled with smart data analytics and cutting-edge measurement technologies, it opens up new opportunities for more efficient vehicle production.
Robert Engelhorn, Director of BMW Group Plant Munich, is working to advance the application of these technologies: “At Plant Munich, it takes about 30 hours to manufacture a vehicle. During that time, each car we make generates massive amounts of data. With the help of artificial intelligence and smart data analytics, we can use this data to manage and analyse our production intelligently. AI is helping us to streamline our manufacturing even further and ensure premium quality for every customer. It also saves our employees from having to do monotonous, repetitive tasks.” As with any innovation, the key factor is effectiveness: “Our team in production are highly experienced specialists, so they are the best judges of whether an AI application can boost quality and efficiency at any given stage of production,” says Robert Engelhorn.
The options for using AI and smart data analytics are currently being tested in various areas of BMW Group Plant Munich. In some areas, the technologies are already in use in series production, such as the press shop and function validation.
Smart Data and AI in the press shop
The press shop at the BMW Group’s home plant in Munich turns more than 30,000 blanks a day into vehicle body parts. Since 2019 each blank has been given a laser code at the start of production so the body part can be clearly identified throughout. This code is picked up by the iQ Press system, which records material and process parameters – such as the thickness of the metal and oil layer, and the temperature and speed of the presses. The parameters are then related to the quality of the parts produced.
Uploaded to the cloud in real time, the data is immediately available in its entirety for the production team to gain a clearer picture of the manufacturing process. iQ Press data is an important tool for them, as it eliminates the need for each body part to be checked in minute detail, in quality control for example, and picks out only irregularities that require action.
Artificial intelligence also offers potential to identify recurring patterns in a process, based on the data collected, to support continuous optimization. So, as well as improving the efficiency of production systems, iQ Press helps to further increase hourly output from the press shop.
Predictive maintenance in the body shop
Body shop robots are fitted with a combined total of over 600 welding tongs. If the tongs ever need replacing unexpectedly, it costs significant time and money. Moreover, many of the robots are difficult to access, so dismantling and replacing their tongs can take hours.
Until now, the condition of tongs has been monitored by eye, by a member of the production team. But in recent months, the maintenance specialists at Plant Munich have been fitting sensors to all the tongs to measure friction levels three times per shift and report any abnormalities. The data they produce is constantly evaluated by software, allowing potential machine failures to be predicted. Martin Hilt, Innovation and Digitalisation Officer at Plant Munich, explains: “Because we have the sensors and collect their data in a cloud, we can now monitor round-the-clock whether any maintenance work is needed. So, we can plan any replacements better and potentially schedule them for a production break.”
Dust particle analysis in the paint shop
Despite comprehensive cleansing systems, vehicle bodies can pick up dust particles as they make their way to the paint line. Though invisible to the human eye, the particles can affect the quality of the finish. Until now, potential defects have gone undiscovered after the painting process, revealed only by the automatic surface inspection. They then had to be reworked, or the bodies repainted completely.
Now, however, every paint shop system incorporates sensors that measure dust levels and allow the quality of paintwork to be predicted. “We can now tell quickly if the environmental parameters are not quite right at some point, either within the paint shop or in one of the buffer areas. It takes a lot of data to do this, which we collect throughout the process, evaluate historically and analyse in real time,” explains Martin Hilt.
Over the last few months, a further special sensor developed by Plant Munich has been measuring dust levels on body parts at the beginning of the painting process, before and after the emu feather rollers. In the future, when dust levels are too high, car bodies will pass through the paint shop untreated and be sent for further cleansing.
AI-based image recognition in assembly
AI projects in assembly mainly focus on automated image recognition. Here, the technology is used to evaluate images of a component and compare them in milliseconds with hundreds of other images from the same sequence. The system then identifies any deviations from the norm, such as parts that are incorrectly positioned or fitted, or absent.
At Plant Munich, automated image recognition allows the production team to identify whether the hazard warning triangle, wiper caps and door sills have all been correctly fitted to each car. Previously, small bubbles in the foil cover of a door sill were often enough to prevent the conventional camera gates from seeing if the logo on the door sill was correct. But now an associate photographs each part concerned in turn and can even use the mobile equipment to check parts that are more difficult to access. Distance, angle and light hardly have any effect on AI evaluations, which reveal within fractions of a second whether everything is in place or not.
The AI system is trained by associates. They start by photographing the component concerned from various perspectives and marking potential deviations on the images. This allows them to develop an image database that can be used to build up a neural network for evaluating the images. Evaluations are carried out fully automatically, and the machine decides by itself whether or not a part meets all the specifications.
RFID identifies components in the vehicle
Radio Frequency Identification (RFID) allows components to be identified automatically and contactlessly throughout the value chain. “Our goal is to save production workers from having to scan components manually, and simultaneously to streamline manufacturing even further by ensuring the right components are fitted to the right vehicles,” says Martin Hilt. RFID is currently being used in seat production at Plant Munich but will soon be used throughout the vehicle assembly as well.
Smart RFID labels required for the system are applied before the component leaves the supplier. They remain in place throughout production, allowing line-side antennae to pick up every labelled component within each car as it passes.
Function validation with the Comfort Access robot
Comfort Access was first introduced in the current BMW 3 Series. A small team from Electrics/Electronics Validation in Munich has now developed a special robot to validate its integration.
Vehicles with Comfort Access use three exterior antennae to generate a three-dimensional electromagnetic field around the car. When the driver enters the field, the system recognises the car key. At about 3 metres from the car, it switches the Welcome Light on to illuminate the area outside the driver’s door. At about 1.5 m, the doors unlock – and relock automatically if the driver walks away.
Until now, this special feature has been validated manually, with parameterisation in development alone taking two days per vehicle. The Comfort Access zones and the influence of production processes on them are then checked manually again in the plant, before production begins, taking into account the various country-specific requirements and equipment features, such as trailer couplings. All in all, it is a lengthy process and not always entirely accurate, given the multitude of different functions.
To solve the problem, the BMW Group and the University of Applied Sciences (HTW) in Dresden have developed a measurement robot that autonomously circles the vehicle several times in a pre-defined pattern to determine the strength of the magnetic field at various required points. Attached to the robot is a box containing the car key. The box can be set at different heights to reflect the different ways a driver might carry it: in their hand, their sports bag or a breast pocket, perhaps. As soon as the robot detects the vehicle electronics locking or unlocking the doors, its inbuilt Lidar scanner measures the distance between the key and the vehicle, and surveys the vehicle’s surroundings. The data that is generates goes straight to a central computer, where it is portrayed as a graphic.
The advantages of the system are obvious: “This robot is not only much faster, it’s also more precise. The results we obtain are highly detailed and, most importantly, objective. So we can even start validating the function before the car has its first test-drive,” explains Martin Hilt.
Vehicle location in the production system
The specialists responsible for product integration at Plant Munich ensure stable processes to deliver defect-free vehicles throughout. They are also responsible for integrating pre-series vehicles into production to allow a smooth official production launch with series quality right from the start.
“Since the start of this year, our specialists have been using a new app that notifies them as soon as the pre-series vehicle they are tracking reaches a specified point in assembly. It allows them to locate any car they want – so they can check, say, a particular combination of equipment features,” says Martin Hilt.
The new app not only replaces the manual process but also improves validation. In the future, it can also be used on series vehicles.
BMW Group wins “Connected Car Award” for use of artificial intelligence in production
On 7 January, the magazines Auto Bild and Computer Bild presented the BMW Group Production with their Connected Car Award in the Pioneer category. The winner is selected by a jury of experts comprised of editors from both publications, honoring particularly innovative solutions, such as the use of artificial intelligence in production. The BMW Group has been applying AI solutions in several use cases in series production for some time now. One example: In the final inspection area at the Dingolfing plant, vehicle order data is compared to a live image of the model designation of the newly produced car. If live image and order data don’t match, if e.g. a designation such as “xDrive” is missing, the workers carrying out the final inspection receive a notification.
Dirk Hilgenberg, Senior Vice President Production System, Technical Planning, Tool Shop, Plant Construction at the BMW Group, accepted the award at CES in Las Vegas. He stated: “We are delighted to receive this very special award. It confirms that we are on the right track, introducing effective applications that create added value for the production system and provide maximum support for our employees.”
The BMW Group’s Intranet of Things platform in particular ensures a smooth integration of new AI applications into production IT. Workers can choose the most suitable tools from a digital toolbox, combine them into their own solutions and install them via plug and play. In December 2019, the BMW Group publicly shared parts of its innovative digital image tagging software, which has been successfully applied in various AI applications. In turn, software developers all around the world support the development of AI software, allowing the automaker to focus primarily on the advancement of specific AI applications in production and logistics.
Connected, flexible, autonomous: BMW Group expands use of innovative technologies in production logistics
The BMW Group is increasingly relying on innovations from the fields of digitalisation and Industry 4.0 in production logistics. This will ensure the company’s global production network continues to receive the parts it needs in a timely and reliable manner in the future. The focus is on applications such as logistics robots, autonomous transport systems at plants and digitalisation projects for an end-to-end supply chain. Staff can control logistics processes from mobile devices such as smartphones and tablets and use virtual reality applications to plan future logistics. Innovations coming out of many pilot projects are being implemented worldwide in logistics at BMW Group plants.
“Logistics is the heart of our production system. Our broad spectrum of ground-breaking projects helps us run increasingly complex logistics processes efficiently and transparently,” according to Jürgen Maidl, head of Logistics for the BMW Group production network. “We are taking advantage of the wide range of available technological innovations and working closely with universities and start-ups. We are already working with tomorrow’s Industry 4.0 technologies today.”
Around 1,800 suppliers at more than 4,000 locations deliver over 31 million parts to the 30 BMW Group production sites worldwide every day. Digitalisation and innovations help the company organise logistics more flexibly and more efficiently. At the same time, almost 10,000 vehicles coming off the production line daily must be delivered to customers around the globe. Digitally connected delivery, so-called Connected Distribution, ensures that these transport routes are also more transparent.
Connected Supply Chain: Full data transparency in the supply chain
The BMW Group supply chain relies on a global supply network and close cooperation with numerous logistics service providers. The Connected Supply Chain (CSC) programme significantly increases supply chain transparency. It updates the plants’ material controllers and logistics specialists on the goods’ location and delivery time every 15 minutes. This transparency enables them to respond immediately if delays appear likely and take appropriate steps early to avoid costly extra runs.
Autonomous transport systems both inside and outside
Autonomous transport systems such as tugger trains or Smart Transport Robots are increasingly used to transport goods within production halls.
To allow tugger trains to now also be used for the sophisticated process of supplying assembly lines, as part of a pilot project, BMW Group Plant Dingolfing has developed an automation kit, which enables conventional tugger trains of any brand already on hand to be upgraded to autonomous tugger trains. The capabilities of these driverless tugger trains go beyond automation of earlier solutions.
Another future technology is also being piloted alongside autonomous tugger trains at the Dingolfing plant. A Smart Watch supports logistics staff during the container change process and announces approaching tugger trains via a vibration alarm. The employee can also read which containers should be unloaded and send the tugger train on to its next destination by tapping the display.
The BMW Group is also pioneering the use of autonomous transport systems outdoors. As part of a pilot project, the BMW Group is using an autonomous outdoor transport robot for the first time at its Leipzig plant to bring truck trailers from where they are parked to the unloading and loading bay on their own. A mobile platform drives underneath the trailer, connects it and steers it through the plant. The so-called AutoTrailer, with a payload of up to 30 tons, navigates by laser, without additional guidelines or markings, through the plant’s outdoor areas. Sensors and cameras provide a 360° all-round view, which forms the basis of the safety concept.
The huge potential of this transport system is particularly evident at the BMW Group’s largest plant in Spartanburg, where about 1,200 of these trailer-shunting manoeuvres take place every day.
Back in 2015, the BMW Group joined forces with the Fraunhofer Institute IML to develop the first self-driving Smart Transport Robots (STR) for transporting roll containers through logistics areas within production halls. The second generation is now in operation at BMW Group Plant Regensburg. The flat robots carry roll containers weighing up to one ton and transport them autonomously to where the goods need to be. They calculate the ideal route independently and move freely through space. A built-in battery module from the BMW i3 powers the STR for a whole work shift.
Loading and unloading of goods containers:
Robots take over arduous tasks and relieve staff
After delivery to the plant, the goods are transported to the assembly line in containers and parts containers of various sizes. For the tiring job of reloading containers from pallets onto conveyor belts or into storage, employees will be assisted in the future by logistics robots specially developed for this purpose. Four different types of robots, referred to as “Bots” by logistics experts, are currently being tested or have already been integrated into series production.
The lightweight robots take on different jobs: they can take full plastic boxes from the pallet in the incoming goods area and place them on a conveyor system, they do unload tugger trains and place boxes loaded with goods on a shelf, they collect various small parts from appropriate supply racks and they stack empty containers on pallets before they re-enter circulation.
Using artificial intelligence, the robots can detect and process various different containers and determine the ideal grip point.
Smart devices support logistics staff in paperless logistics
Gloves with integrated scanners and displays, data glasses and smart watches are increasingly used to support logistics employees. The transition to paperless logistics, with digitally labelled containers and shelves, opens up new areas of application for mobile devices. Glove scanners read the electronic label and indicate the exact contents of the small load carrier on a small display that can be worn on the arm.
Virtual reality and artificial intelligence
The use of virtual reality already plays an important role in planning logistics spaces. In a virtual environment, planners can quickly and efficiently lay out future logistics areas completely and assess how much space is needed, for instance. Planning is based on 3D data representing the real structures of a logistics hall. For the past several years, the BMW Group has been capturing its plants in digital form with millimetre accuracy, using special 3D scanners and high-resolution cameras. This creates a three-dimensional image of the structures, so that manual recording on site is no longer needed. When planning future logistics areas, BMW Group experts can now combine existing data with a virtual “library” of shelves, lattice boxes, small load carriers and around 50 other widely-used operating resources.
Connected Distribution:
Vehicle delivery transparency from plant to showroom
Like delivery of parts to plants, the transport of vehicles to the dealership is now also digitally and transparently traceable. The former Connected Distribution pilot project was fully integrated into series production this year. The system uses the same IT built into BMW Group vehicles to track the location of finished vehicles once they are ready to leave the plant. The vehicle transmits its current geolocation and status to the logistics centre via a mobile connection every time it is switched off.
Focus on sustainability: Natural gas, electric and future hydrogen trucks will reduce CO2 emissions
Logistics can help the BMW Group achieve its sustainability goals. The focus here is on continuous expansion of CO2-efficient modes of transport. More than 60 percent of all new vehicles now leave production plants by rail.
Nevertheless, it is still necessary to use trucks on certain in- and outbound logistics routes. To reduce emissions from these truck journeys, the BMW Group is already using natural gas and electric trucks in cooperation with logistics service providers. The aim is to reduce truck emissions by 40% by 2030 and to be completely emission-free by 2050.